
What is the production variance for settlement?
Production variance is not relevant for settlement, only for information. 5.1.3) Planning Variance. Planning variance is the difference between costs on the preliminary cost estimate for the order and target costs based on the standard cost estimate and planned order quantity.
What happens to the production order balance after settlement?
At period end the production order receives a secondary credit that is equal to the variance during settlement, resulting in zero balance. During the settlement process, product cost collectors and process order variance are posted to Profitability Analysis (CO-PA) and FI.
What is the material value I receive from the production process?
Here the material value you receive from the production process is updated as credit in the production order actual costs. The credit value is based on the material price control S or V. Since all our materials have price control S.
How to develop settlement forms for sales rebate settlement documents?
For the sales rebate settlement documents, 2 forms are predefined. You can use the following forms as a template to develop your own forms: Collection Settlement Document (for customer settlement) Output management is now available for the document category "Settlement Documents" in settlement management.
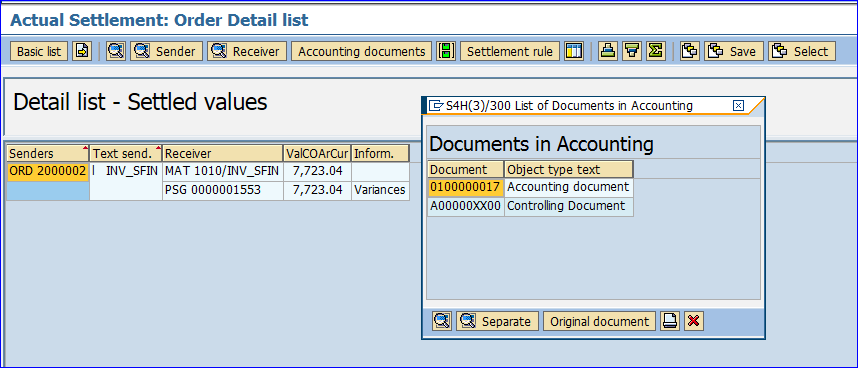
How is production variance calculated in SAP?
Variance = Actual Cost – Actual Cost Allocated (credits) – WIP – ScrapInput price variance.Resource – usage variance.Input quantity variance.Remaining input variance.Mixed –price variance.Output price variance.Lot Size Variance.Remaining Variance.
What is output price variance in SAP?
Output price variances are caused by a difference between the target credit (such as Confirmed Quantity x Standard Price) determined by variance calculation, and the actual credit posted when the goods were received (such as Confirmed Quantity x Moving Price).
What is KKS1 used for?
The SAP TCode KKS1 is used for the task : Variances - Product Cost by Lot (C).
What is variance key?
Key that controls variance calculation. you can define this variace key in OVK1. Define this to plant in OKVW. Variances can only be calculated for the orders for which a variance key has been entered. This key is defaulted through the costing view in the material master record.
What is WIP calculation in SAP?
The WIP calculation function valuates the unfinished products (work in process). In the Product Cost by Order component, the work in process is valuated at actual cost. Work in process is the difference between the debit and credit of an order that has not been fully delivered.
How do you settle a production order variance in SAP?
For the settlement of production orders, you can transfer to CO-PA the variance categories calculated in Cost Object Controlling. The requirements for this are as follows: You are working with standard prices for processed materials. You have already performed variance calculation in Cost Object Controlling.
What does KKAO do in SAP?
KKAO is a transaction code in SAP CO application with the description — WIP Calc.: Collective Processing....KKAO — Meta Data.Description:WIP Calc.: Collective ProcessingMain Category:COSub Category:Cost Object Controlling
What is SAP KKS1?
KKS1 is a transaction code in SAP CO application with the description — Variances - Product Cost by Lot (C). On this page, you will find similar/related TCodes to KKS1, Tables feeding data for this TCode, links to SAP documentation, Wiki and Help pages, discussion threads, and other resources.
What is variance calculation in SAP?
Variance calculation is based on the reconciled planning of internal activity between cost centers and business processes and the costs thereby incurred. Variances are the differences between actual costs and plan costs or target costs.
How do I calculate variation?
Steps for calculating the varianceStep 1: Find the mean.Step 2: Find each score's deviation from the mean.Step 3: Square each deviation from the mean.Step 4: Find the sum of squares.Step 5: Divide the sum of squares by n – 1 or N.
Which formula should be used to calculate the variance?
For a population, the variance is calculated as σ² = ( Σ (x-μ)² ) / N. Another equivalent formula is σ² = ( (Σ x²) / N ) - μ². If we need to calculate variance by hand, this alternate formula is easier to work with.
What is production variance?
Production volume variance is a statistic used by businesses to measure the cost of production of goods against the expectations reflected in the budget. It compares the actual overhead costs per unit that were achieved to the expected or budgeted cost per item.
What is price variance in SAP?
The Purchasing Price Variance or PPV is a warning flag that says that the gross margin will have variance, taking care about the situation, on a nimble way, enable the organization to keep margins going forward. Our scenario is built it to buy 1,000 LB of raw material, where: Standard Cost is 10 USD per LB.
What is output variance?
The output quantity variance is the difference between the actual credits and the target credits, which is the difference between the manually-entered actual costs and the allocated actual quantities.
What is input price variance in SAP?
Input price variance = (Actual price - Plan price) x Actual input quantity. Fixed input price variance = (Fixed actual price - Fixed plan price) x Actual input quantity. Variances caused by both price differences and quantity differences are assigned to the category of input price variances.
What is variance in SAP?
Variances are the differences between actual costs and plan costs or target costs. They are displayed separately for a cost center, for an activity type of a cost center or business process, divided into fixed and variable portions.
What is cost component split?
The cost component split allows a cost estimate to group costs of similar types of components, such as material, labor, and overhead.
What happens when production order activities are confirmed?
When production order activities are confirmed, the production or product cost collector is debited, and the production cost center is credited. There are no FI postings during activity confirmation.
Why is standard cost estimate used in variance analysis?
The Standard Cost Estimate is involved in variance analysis because it is used for stock valuation. When a production or process order delivers production to inventory, it receives a credit based on standard price. Total variance is the difference between actual costs debited to the order and costs credited to the order due to deliveries to stock.
Where are CO costs allocated?
The costs in CO are allocated from overhead cost centers to production cost centers during assessment and then onto production order during activity confirmation.
When are plan costs posted?
Plan costs are posted prior to a fiscal period. Actual costs are posted in real time during a fiscal period.
What is input quantity variance?
Input quantity variance occurs as a result of a difference between plan and actual quantities of materials and activities consumed.
What is preliminary costing in SAP?
When you create a production order in SAP, the system automatically creates a planned cost estimate for that order called preliminary costing. Further, the system calculates the preliminary cost in accordance with the customizing settings in the default values for the order types.
What happens when you post a goods receipt from the production order?
Here the material value you receive from the production process is updated as credit in the production order actual costs. The credit value is based on the material price control S or V. Since all our materials have price control S. Thus, the goods receipt value is equal to the quantity of material confirmed multiplied by the standard price.
What does actual cost in the material ledger represent?
In this way, we can say that actual costs in the Material Ledger represent the actual quantity consumption value at actual prices .
What is simultaneous costing?
Simultaneous costing is the process of capturing actual costs for cost objects, such as manufacturing orders.
What is material ledger actual cost?
On the other hand, the Material Ledger actual costs concept is a periodic calculation. It allocates all the variances of raw material prices, manufacturing process, and overhead cost allocation to stock and consumptions.
