
What is the meaning of the term “settlement” in production?
Settlement is nothing but, While doing production the target cost and actual cost will be saved in prod order. This will be in intermediate stage. In any company FI will follow Debit / Credit principle for accouts management.
How do I settle a production order?
You should the settlement based on the folowing stage of the profuction order : 3.Production Order Technically Complete -TECO if there is not pending job .Other wise duirng settlement it will go to WIP. Then complete the order technically by using T code: CO02---> Functions (Menu) ---> Restrict Processing ---> Technically Complete.
Why is production order settlement necessary for product costing?
Production order settlement is necessary for Product Costing if you want to calculate production cost and variance analysis against standard cost. Help to improve this answer by adding a comment. If you have a different answer for this question, then please use the Your Answer form at the bottom of the page instead.
What is the production variance for settlement?
Production variance is not relevant for settlement, only for information. 5.1.3) Planning Variance. Planning variance is the difference between costs on the preliminary cost estimate for the order and target costs based on the standard cost estimate and planned order quantity.
Why is a production order settlement necessary?
What does it mean when the balance is zero in production order?
What does production confirmation mean?
Can you make GR against a prod order?
Do you have to do a settlement after confirmation?
Do you have to settle a production order with CO88?
See 3 more
About this website
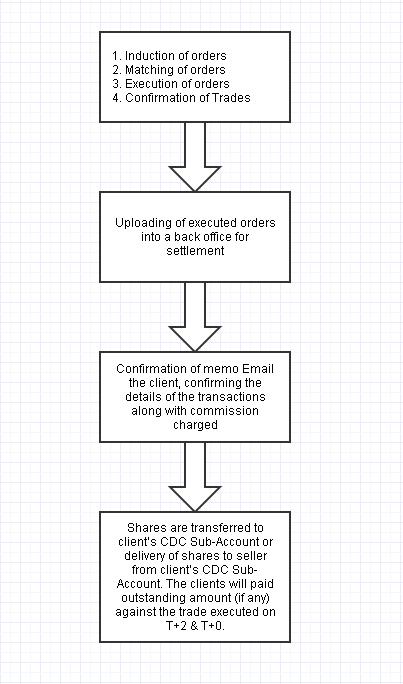
What are order settlements?
Order of Settlement means a writ- ten order issued by the Director termi- nating a civil penalty action. An Order of Settlement does not constitute an agency decision that any violation took place.
How do you settle a production order in SAP?
We would like to see how the following CO Production Order steps are processed within SAP.Creation and Release of a CO Production Order for a specific Material/Plant. ... Updating the Plan Costs on the CO Production Order. ... Issuing Raw Materials to the CO Production Order.More items...•
What is the meaning of production order?
A production order is an order issued within a company to produce a specific quantity of material within a certain timeframe. A production order may be issued pursuant to a sales order, and its issuance triggers a number of events.
What is the purpose of a production order?
A production order is used to define the material to be produced, plant location where production has to be done, date and time of production, and quantity of goods required. A Production Order also defines which components and sequence of operations are to b used and how the order costs are to be settled.
What is a settlement order in SAP?
Use. When a production order is settled, the actual costs incurred for the order are settled to one or more receiver cost-objects (for example, to the account for the material produced or to a sales order).
What is KO88 in SAP?
KO88 is a transaction to settle the Order (Production order, Internal order, QM order, PM order, etc). In case of Production order, if there is any balance lying in the order, it would be on account of WIP or variances.
How do you confirm a production order?
To confirm Production Order, use T-code: CO15. In the next screen, enter Production Order number and click the tick mark. In the new window, enter the yield quantity that shows produce quantity to be declared.
How do you release a production order?
A production order can be changed to the Released state either from the production order or by using a batch process. The production order can also be updated automatically from planned production orders that are firmed by using the Firming time fence field on the Master plan page.
How do you make a production order?
Creating a Production order without referring planned order Step 1 − Use T-Code: CO01 or go to Production → Production Control → Order → Create → with material. Step 2 − Enter the material code for which the production order needs to be created. Enter Plant Code and click the tick mark in above screen.
What is difference between process order and production order?
Process orders provide you with extra functionality, such as phases and process instructions for process industries. If you use production orders, the system transfers a routing and a bill of material (BOM) into the master data of the order header.
What is difference between planned order and production order?
Planned orders are converted into production orders for in-house production and into purchase requisitions for external procurement. In contrast to planned orders, production orders and purchase requisitions are fixed receipt elements, which commit to the procurement.
What are the types of production process?
What are the types of production processes?Mass Production.Batch Production.Job Production.Service Production.Customized Production.
What is a production order document?
A production order is a document that states the number of units to be manufactured, the date when the order is released for production, and where the units should be delivered once they have been completed.
What is difference between process order and production order?
Process orders provide you with extra functionality, such as phases and process instructions for process industries. If you use production orders, the system transfers a routing and a bill of material (BOM) into the master data of the order header.
What is a production order in SAP?
An order to produce a specific quantity of materials within a pre-defined time. It contains all the information required for the actual execution of the production process.
What is the meaning of sales order?
A sales order is a commercial document prepared by a seller and issued to a customer. It confirms the sale of goods or services and details the sale's specifics, including the quantity, pricing, and quality of goods or services provided.
What is Production Order Settlement?
What is Production Order Settlement? Settlement is nothing but offsetting the costs to the FI portion. CO objects carry costs, which needs to be re-assignd to the G/L accounts where it comes from.
TO SETTLE PRODUCTION ORDER | SAP Community
Which Tcode is used to settle the Production Order and how it is done?
Settlement of production order. | SAP Community
Hi Experts, Will anybody please tell me, 1.Why do need to settlte production order. 2.What customization setting require for settlement of production order. 3.How to carry out settlement. Raja.
Settlement Types of Production Orders - Process Orders - SAP
Purpose. The purpose of this page is to clarify the understanding of the system logic concerning the settlement of production orders, process orders and product cost collectors.
What is the default settlement rule?
The default rule for the settlement rule is specified in Customizing for each plant and order type ( transaction OKZ3 or OPL8). If the default rule is PP1, all production orders for this plant and order type receive the FUL rules. If the default rule is PP2, all the production orders for this plant and order type receive PER rules.
What is an unvaluated sales order?
For an unvaluated sales order stock, the sales order always has a CO object, and the goods receipt on the production order is unvaluated. This means that the order is not credited when goods are received. The entire order costs are transferred to the sales order or WBS element.
What is co-production in SAP?
Co-production is when two products are created simultaneously from the input materials. This often takes place in the chemical industry, where an additional product is created with the main product (e.g. in the production of automobile gas from oil). The SAP System differentiates between by-products and co-products.#N#From a technical point of view, co-production is implemented in such a way that the order items receive their own CO objects. This means that instead of a CO object for the production order, you have N + 1 Co objects, so one for the order and N for the N co-products.
How are actual costs and credits posted?
The actual costs and credits are posted on the product cost collector from the goods receipt for different production orders. The deliveries can go to different stock segments if the material has a separate valuation, or if the material is produced in-house or make to order. During settlement, the value of the goods receipts for the period is dynamically calculated for the different stock segments. The actual costs are distributed to the different stocks according to these values. If no goods were received in a period, then the actual costs are posted to a separate price difference account (account modification PRP). For more information, see SAP note 388457.
Is the actual cost of an order settled?
For orders that have not yet been finally delivered or technically completed, the actual costs are not settled. The balance remains on the order.
Is a production order unvaluated?
If a production order has a 100% rule for settlement to sales order/project, then it is unvaluated sales order stock/project stock. In this case, the order is treated like an internal order, meaning that it is settled periodically to the sales order or project, regardless of the status.
Is make to stock inventory debited?
The make-to-stock warehouse inventory is not debited. Instead, make-to-order production is debited.
What happens when production order activities are confirmed?
When production order activities are confirmed, the production or product cost collector is debited, and the production cost center is credited. There are no FI postings during activity confirmation.
What is cost component split?
The cost component split allows a cost estimate to group costs of similar types of components, such as material, labor, and overhead.
When are plan costs posted?
Plan costs are posted prior to a fiscal period. Actual costs are posted in real time during a fiscal period.
Where are CO costs allocated?
The costs in CO are allocated from overhead cost centers to production cost centers during assessment and then onto production order during activity confirmation.
Why is a production order settlement necessary?
Production order settlement is necessary for Product Costing if you want to calculate production cost and variance analysis against standard cost.
What does it mean when the balance is zero in production order?
There is no status update after settlement in production order, If the balance is zero means order is settleed .
What does production confirmation mean?
Production Confirmation : Means the quantities & costs are updated that were occurred during the production
Can you make GR against a prod order?
Upon confirmation of prod order, you can make the GR against it.
Do you have to do a settlement after confirmation?
Yes, after confirmation, you need to do settlement of the Order. Production Confirmation : Means the quantities & costs are updated that were occurred during the production. Settlement means : your posting all the incurred costs to the restive accounts, with Planned data & actual data.
Do you have to settle a production order with CO88?
If you have a different answer for this question, then please use the Your Answer form at the bottom of the page instead. Yes you should do settlement after confirmation of Production order by KO88 for single order and by CO88 for multiple orders.
